In the rapidly evolving manufacturing industry, adaptability and innovation are not just advantages—they are essential for survival. One of the critical aspects of manufacturing is process diversification. From prototype development to mass production, the ability to flexibly apply various processes not only addresses the unique needs of different projects but also bridges the gap between concept and product, turning ideas into reality.
The Essence and Evolution of Manufacturing
At its core, manufacturing is the transformation of ideas into tangible products. Historically, the focus of manufacturing was on mass production, emphasizing efficiency and uniformity. However, with advancements in technology and shifting market demands, the emphasis has shifted toward customization, precision, and scalability. This shift requires manufacturers to leverage diverse processes to meet a wide range of challenges and demands.
The Connection Between Prototypes and Products
Prototype manufacturing is the first step in bringing concepts to life. It serves as a crucial tool for validating designs, optimizing workflows, and ensuring functionality. Prototypes allow designers to identify potential flaws early, improve performance, and save on costs in later stages.
Mass production, on the other hand, takes these validated designs and scales them to meet market demand. The seamless transition from prototype to mass production relies on flexible processes and a deep understanding of the product’s requirements. Whether for small-batch production or large-scale manufacturing, adjusting processes to suit the project is critical.
How Different Processes Meet Diverse Needs
Every project is unique, requiring a tailored combination of processes to achieve its goals. Diversifying manufacturing processes is key to achieving both flexibility and precision. Here are some core processes and their applications:
CNC Machining: Ideal for high-precision components, especially in aerospace, automotive, and medical industries. CNC machining delivers complex designs with tight tolerances, making it a staple for both prototypes and finished products.
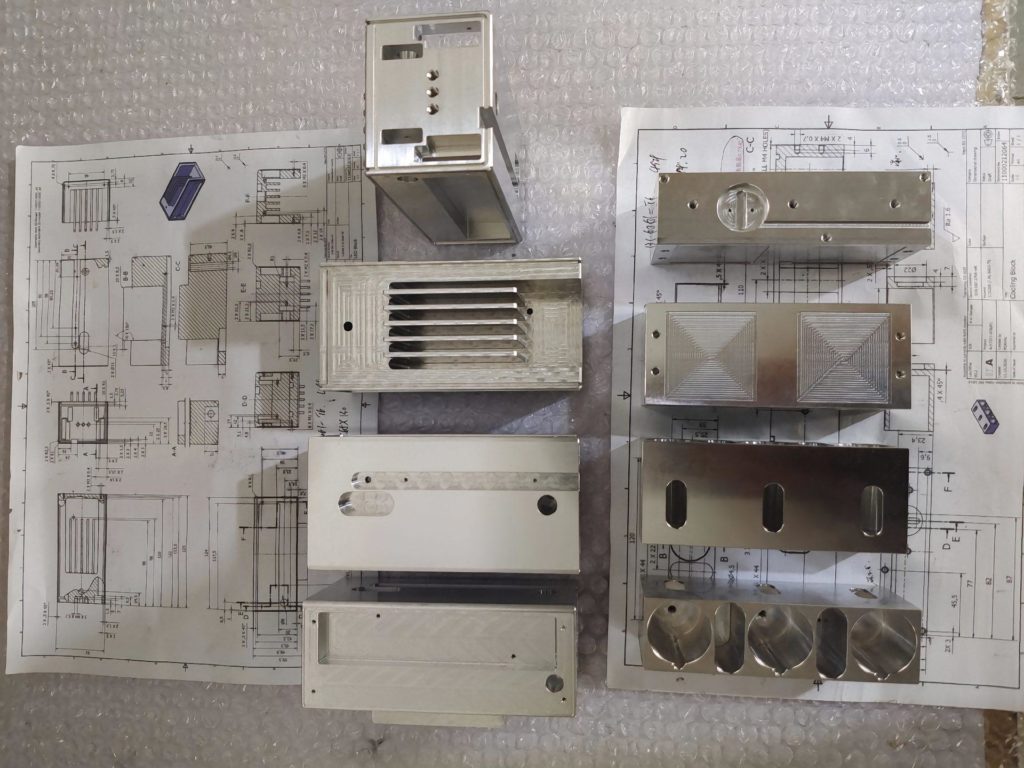
3D Printing: Excellent for rapid prototyping and small-batch production, 3D printing excels at creating complex geometries and significantly reduces lead times.
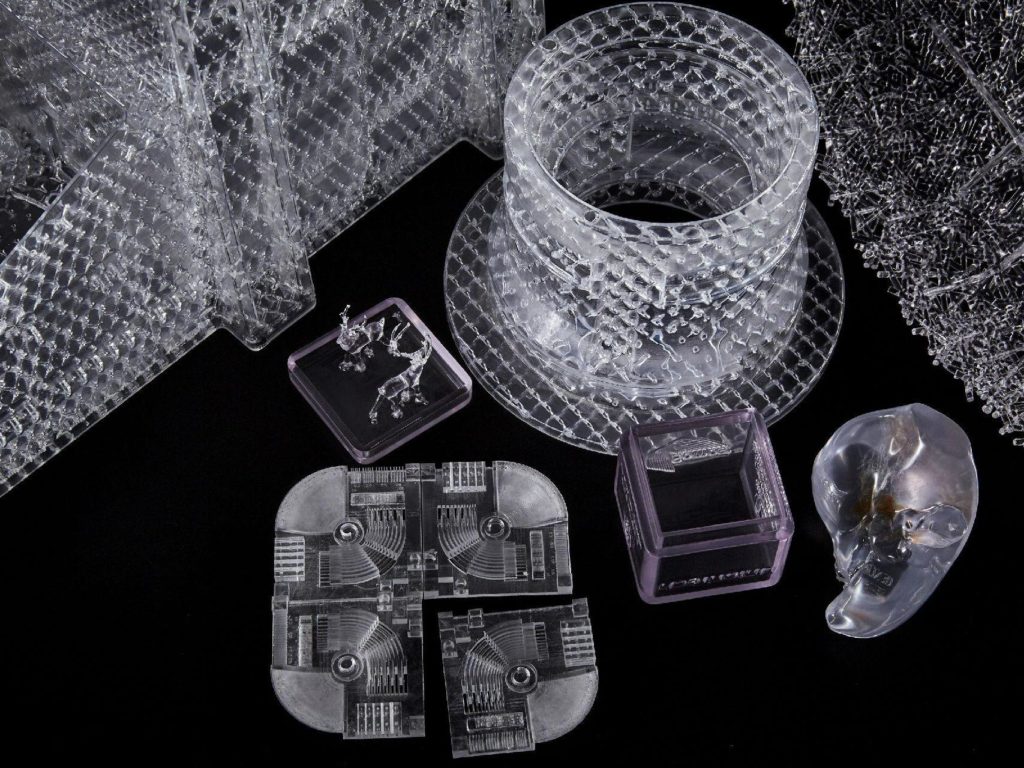
Injection Molding: Best suited for large-scale production, injection molding offers consistency and efficiency, particularly for plastic components.
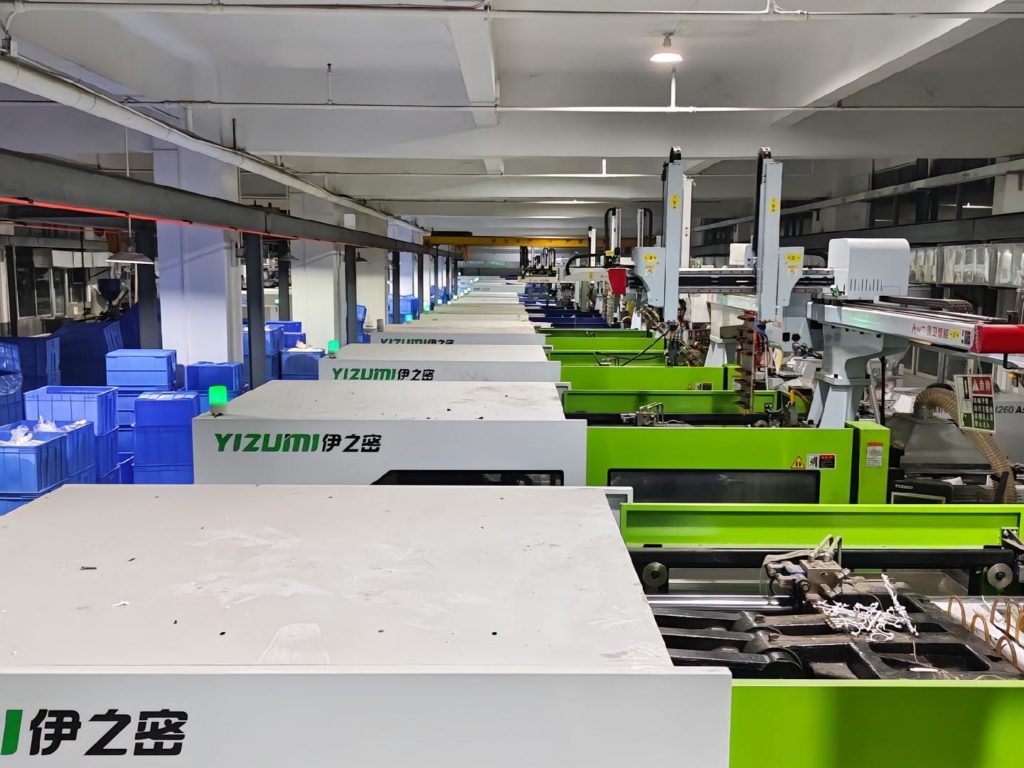
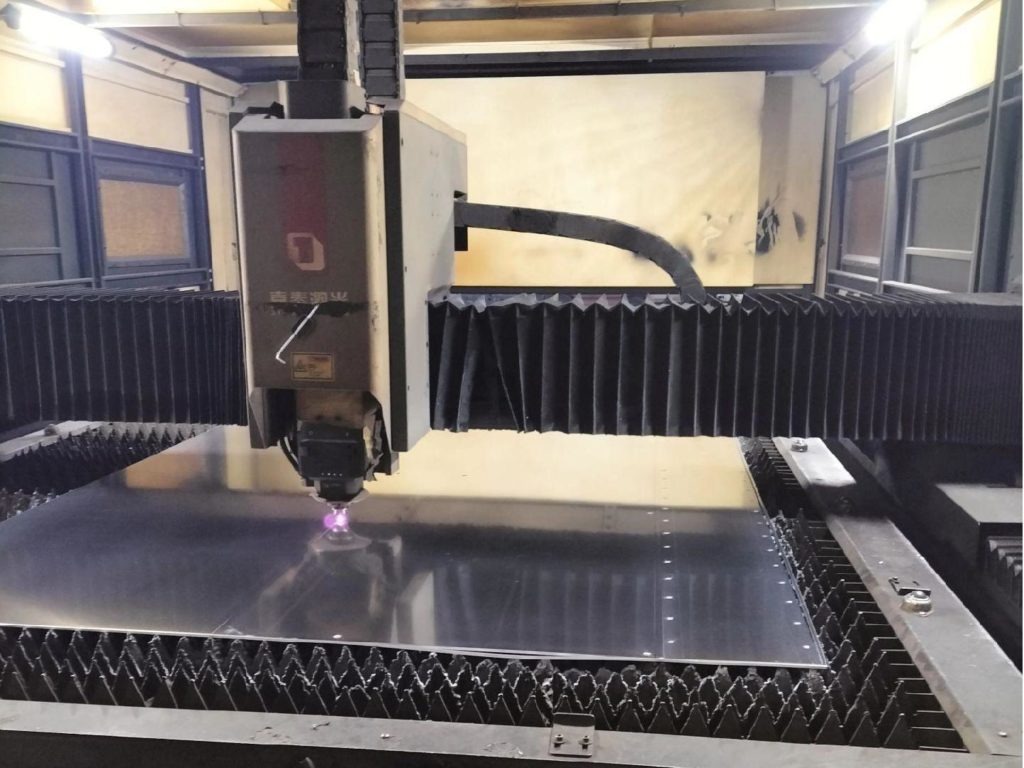
Sheet Metal Fabrication: Highly versatile in both prototype and finished product manufacturing, this process can produce a wide range of metal shapes and designs.
Die Casting: Particularly useful for high-strength, high-complexity metal components. Commonly used in automotive and electronics industries, die casting delivers high precision and smooth surfaces, making it ideal for mass production.
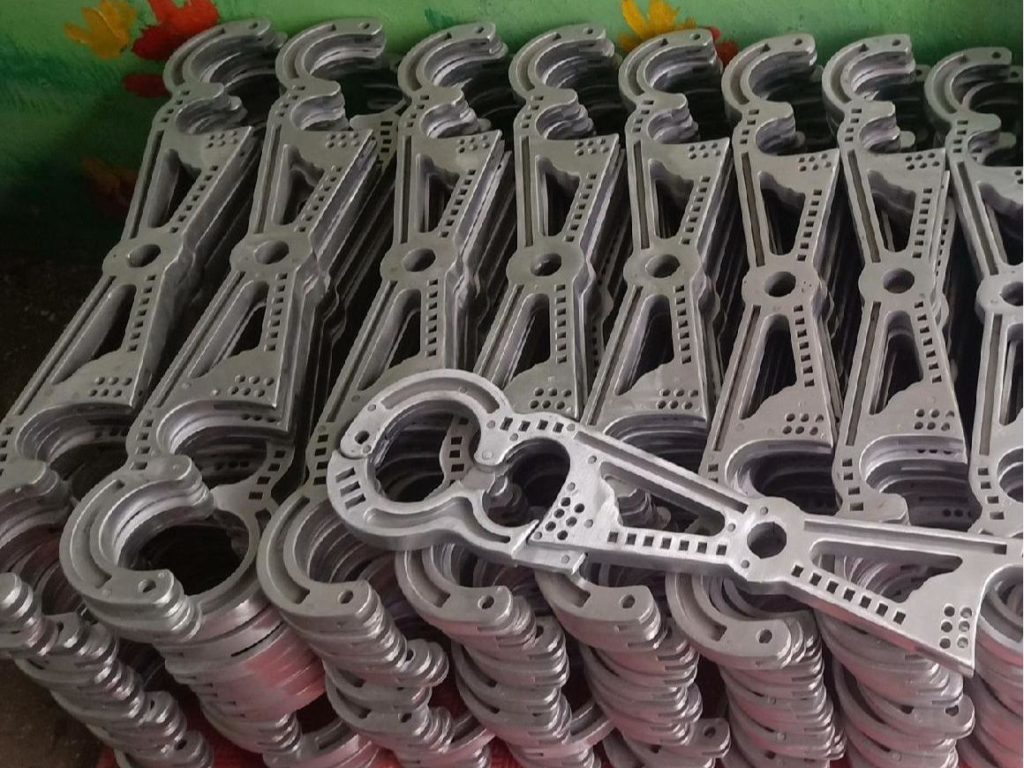
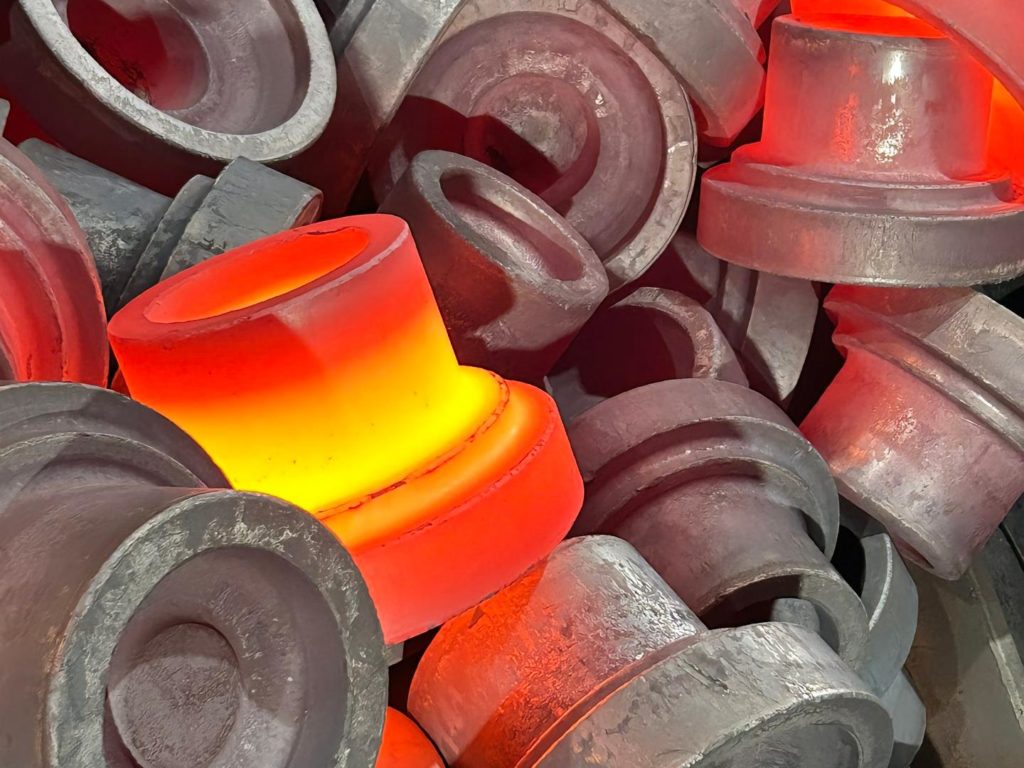
Forging: Known for its exceptional mechanical properties, forging is ideal for manufacturing high-strength, durable metal parts. This process is widely used in aerospace and heavy industries and can cater to both prototypes and mass production.
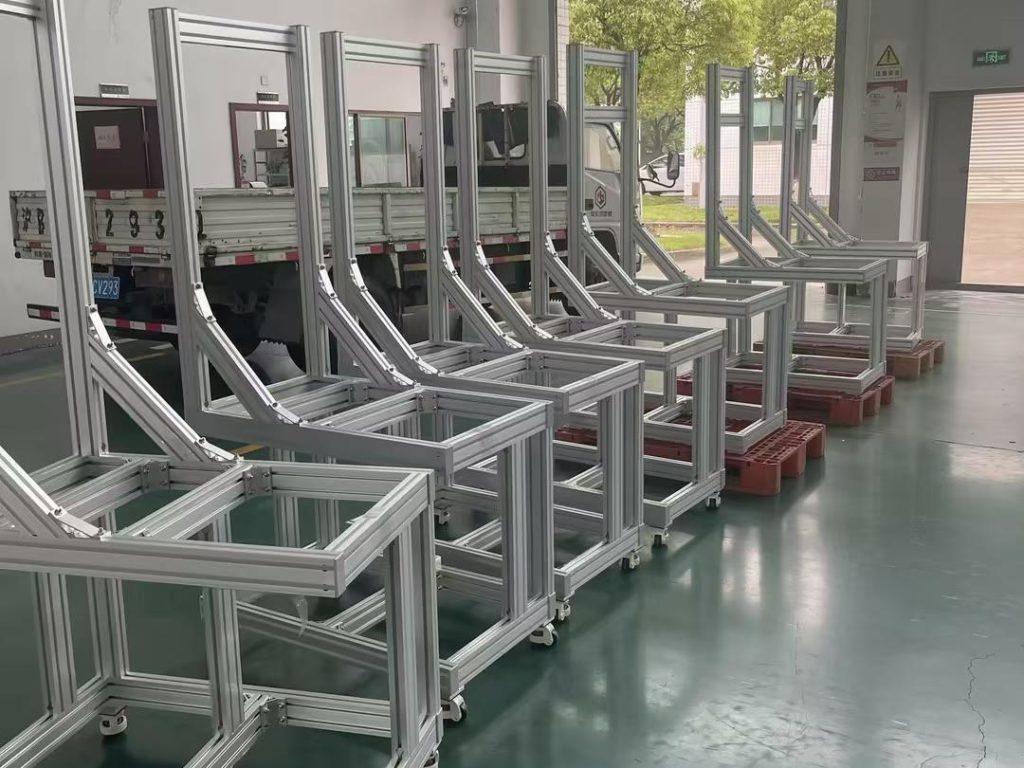
Profile Manufacturing: Processes like extrusion and rolling are excellent for producing metal profiles with standardized cross-sections. This is particularly advantageous for creating aluminum frames, supports, and other structural components in large volumes, with cost-efficiency and high productivity.
Surface Treatments: Processes like anodizing, polishing, and coating ensure that the final product meets aesthetic and functional requirements.
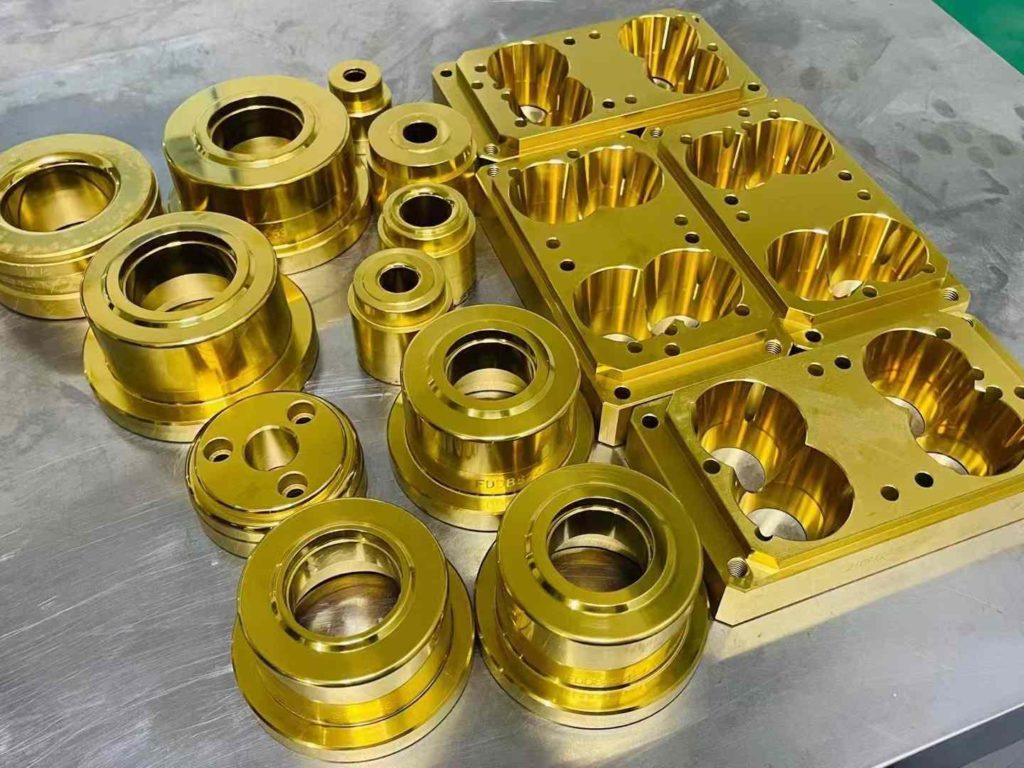
By leveraging these processes effectively, manufacturers can address challenges related to cost, materials, and design complexity.
A Future Built on Diversity
As markets demand faster innovation cycles and greater customization, process diversification will continue to be a cornerstone of successful manufacturing. By mastering a wide range of processes, manufacturers can not only enhance product quality but also adapt to changes in the industry.
In conclusion, the journey from prototype to mass production is a dynamic process that hinges on the diversification of manufacturing techniques. Whether it’s crafting unique prototypes or scaling them into market-ready products, choosing and integrating the right processes is the key to thriving in today’s competitive manufacturing landscape.