In precision manufacturing, surface roughness is a critical parameter for evaluating the quality and functionality of a product. The surface roughness parameters play a vital role in determining the performance, aesthetic appearance, and lifespan of components. Whether in metalworking or other material processes, having a clear understanding of surface roughness and its measurement terms is essential for ensuring that products meet the required specifications.
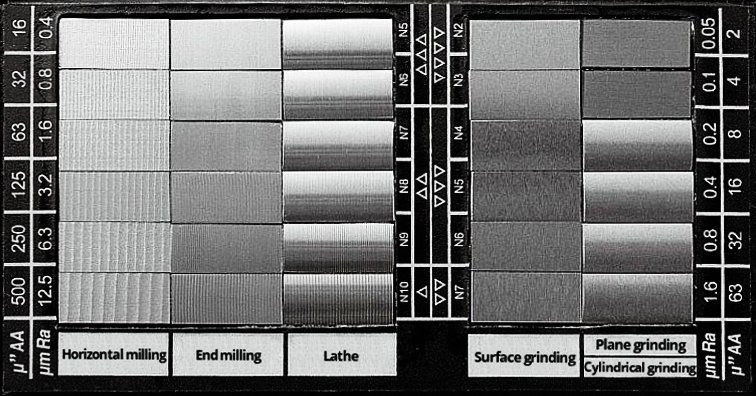
What is Surface Roughness?
Surface roughness refers to the fine, microscopic irregularities on the surface of a material, typically consisting of tiny peaks and valleys. These features arise from the manufacturing process, and their magnitude can significantly impact the material’s performance. For example, a smoother surface may be more resistant to corrosion, while rougher surfaces may offer better friction properties.
Key Surface Roughness Terms
1. Arithmetic Average Deviation (Ra)
- Definition: Ra is the arithmetic mean of the absolute values of the profile deviations from the mean line within a sampling length (L). It is one of the most commonly used surface roughness parameters.

Where z(x) is the deviation of the profile at a given point, and L is the sampling length.
2. Ten-Point Height (Rz)
- Definition: Rz is the sum of the average of the five highest-profile peaks and the five deepest valleys over the sampling length.

Where Zpi is the height of the i-th highest peak and Zvi is the depth of the i-th deepest valley.
3. Maximum Profile Height (Ry)
- Definition: Ry is the maximum distance between the peak line and the valley line within a sampling length. This parameter indicates the greatest fluctuation in surface roughness.
4. Spacing of Profile Micro-Irregularities (Sm)
- Definition: Sm refers to the average spacing between the peaks and valleys over the sampling length. It is a critical parameter that helps in evaluating the texture of a surface.

5. Profile Peak Spacing (S)
- Definition: This is the length of the line segment between two adjacent peaks, projected onto the mean line. It provides insights into the density of the surface texture.

6. Profile Bearing Length (ηp)
- Definition: ηp is the ratio of the bearing length (the portion of the profile that supports the load) to the sampling length (L). It gives a comprehensive view of the surface’s ability to bear loads and its overall functionality.
7. Profile Bearing Length Ratio (tp)
- Definition: tp is a dimensionless parameter that reflects the bearing length’s ratio to the sampling length, providing a generalized measure of the surface condition.

Surface Roughness Symbols and Their Significance
When it comes to labeling surface roughness, several symbols are used to denote the method of surface generation and the applicable roughness parameters. Below are some commonly used symbols:
Basic Symbol (Ra): This indicates that the surface can be produced by any method. If no other roughness parameters or specifications are provided, this symbol is often used for simplified labeling.
Symbol with a Line (Ra-): This symbol indicates that the surface is obtained through material removal processes such as turning, milling, drilling, grinding, polishing, or electrical discharge machining (EDM).
Symbol with a Circle (RaO): This denotes surfaces created through processes that do not remove material, such as forging, casting, stamping, hot-rolling, cold-rolling, and powder metallurgy, or surfaces kept in their original state from the previous processing stage.
Symbol with a Line and Circle (RaC): Indicates that the surface has uniform roughness characteristics, regardless of the method used to obtain the surface.
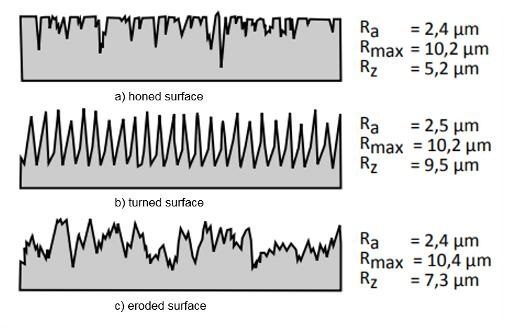
Measuring and Assessing Surface Roughness
To measure and assess surface roughness accurately, appropriate tools and instruments must be used. Instruments such as optical microscopes, electron microscopes, and laser interferometers are common in precise measurements.
During the measurement process, ensure that:
- The surface is clean and free of contaminants.
- The correct measurement direction is chosen to avoid errors from surface waviness or shape deviations.
- Repeated measurements are taken to ensure accuracy and consistency.
Conclusion
Understanding and measuring surface roughness is essential in precision manufacturing. Proper knowledge of terms like Ra, Rz, Ry, Sm, and others allows manufacturers to assess surface quality and meet the specific needs of customers. Surface roughness directly impacts the performance and aesthetic appeal of a product, and precise control over these parameters ensures that products function optimally and meet quality standards.
At AMP Precision, we specialize in providing high-quality precision machining services, including surface finish assessments and custom solutions tailored to your specific needs. By understanding the impact of surface roughness on your products, we can help optimize their performance and longevity. For more information or to discuss your project requirements, feel free to contact us today!